Research
•Towards a concrete circular economy
Why reuse concrete?
Today, almost all concrete removed from existing buildings is crushed and used as a loose material as fill, in road bases, for land reclamation, and aggregates. While this is positive as it reduces the need for virgin materials, could we be making better use of this material? There’s a significant opportunity to rethink our approach and reuse this material instead of downcycling it.
As reinforced concrete contains cement and steel, two of the most energy-intensive structural materials in common usage, there is great potential for saving. The eCO2 emissions per kilo of reused concrete are estimated[1] to be 60% less than that of comparable new reinforced concrete, and less than that of some quarried stone.
Cutting existing reinforced concrete elements into usable units to use instead of in-situ concrete or loadbearing stone will result in carbon savings, with the added benefit of reusing material already processed, rather than extracting more natural resources.
Applications for reused concrete
Concrete sections salvaged from existing buildings can be saw cut into planks, strips and blocks ready for reuse in a variety of ways in new structures.
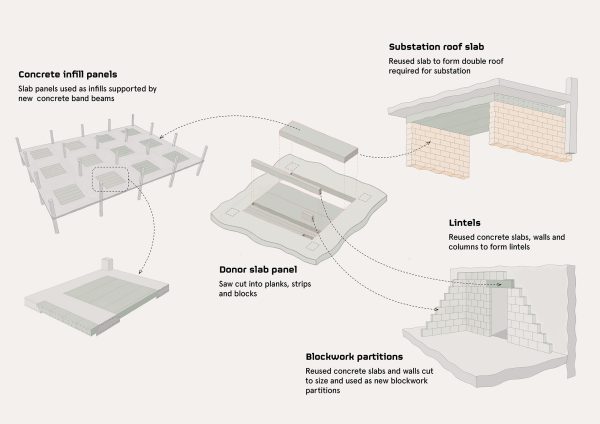
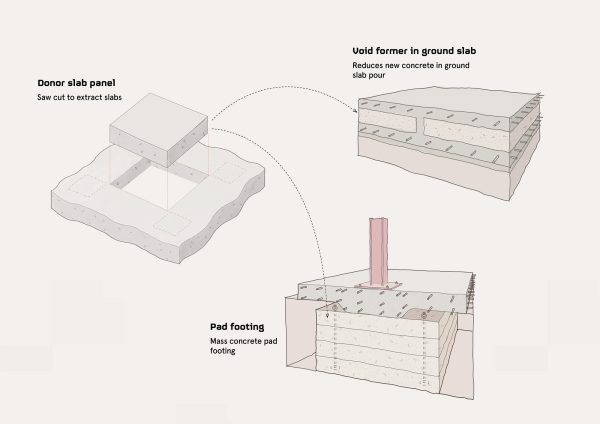
Reused concrete in practice
Despite the abundance of concrete buildings, reuse of structural concrete is still an emerging practice with few pilot-scale case studies. At HTS, we’re exploring options for concrete reuse on several projects with the aim of realising them on site.
On a commercial mixed-use development in Camden, the design of the new building incorporates ‘soft spots’ – areas of the floor that can be opened up in future without compromising the structure, part of an enhanced tenant offering and a ‘long life loose fit’ design approach. These soft spots are an ideal opportunity to reuse concrete from the donor building, instead of new precast elements. Our pre-reclamation audit has identified reusable concrete planks from the existing building and, with the help of a demolition contractor, proposed a methodology to reclaim and incorporate them into the new build. Full implementation of the strategy is estimated to save 27 tonnes of embodied carbon.
Challenges and considerations: for the reuse of concrete to be achievable in practice on an urban commercial development, it is important to consider:
- 1 Deconstruction - can elements be salvaged in the right sizes and without incurring damage?
- 2 Handling - the dimensions of salvaged elements can be influenced by site constraints, crane access and transport methods
- 3 Storage - salvaged elements could be stored on site, at a contractor’s yard or (in future) at a dedicated site for reclaimed materials
- 4 Testing - material and condition testing and design checks to verify that salvaged elements have the properties and quality required for reuse
- 5 Cost - The deconstruction, handling and storage of elements makes this process more involved and can introduce more cost as a result
While the technical feasibility of reusing concrete has been demonstrated in a few examples, the economic viability remains to be explored. We are targeting small pilot projects such as the soft spot infill in Camden to trial the process, understand how to overcome the barriers to then scale up the reuse of concrete to have a meaningful impact.
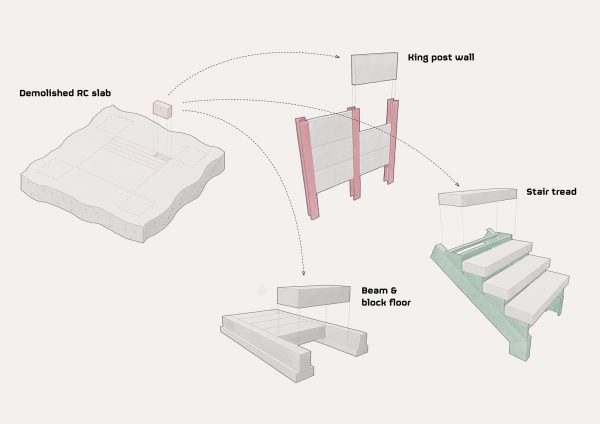
[1]In research by the Structural Xploration Lab, EPFL