Series
•How we made it: 76 Southbank
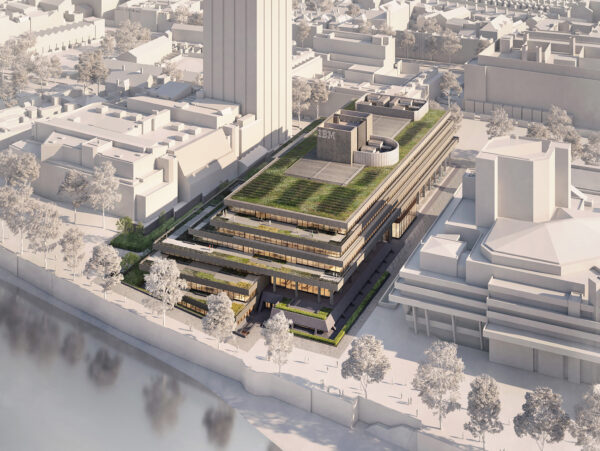
The project
Denys Lasdun’s iconic Grade II listed design, originally constructed as IBM’s London office in 1981, has undergone a sensitive redevelopment and extension. The addition of one storey and extension over existing terraces has increased its floor area by 40%, while preserving 80% of the concrete volume, safeguarding the building’s distinctive aesthetic while also reducing carbon. Additionally, the new lift core and entrance has added to the creation of a modern, adaptable, low-carbon workspace.
- Location: Southwark, London
- Client: Wolfe Commercial Properties Southbank
- Architect: Allford Hall Monaghan Morris
- Size: 38,850 m2 GIA
- Stage: On site
- Time Frame: 2018-2025
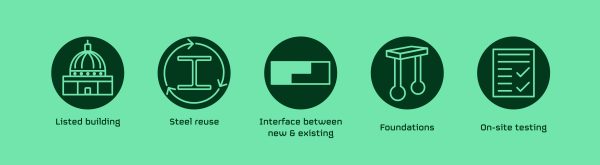
The process
Listed building:
The building was Grade II listed during the planning application meaning the scheme had to be adapted to retain the original brutalist aesthetic while delivering the increased floor area.
Steel reuse:
Reused steel was selected using the HTS Stockmatcher tool, the reclaimed steel was used in the new exposed feature lift core. Of 230 tonnes of new steel overall, 24 tonnes was from reclaimed stock saving approximately 45tonnes CO2.
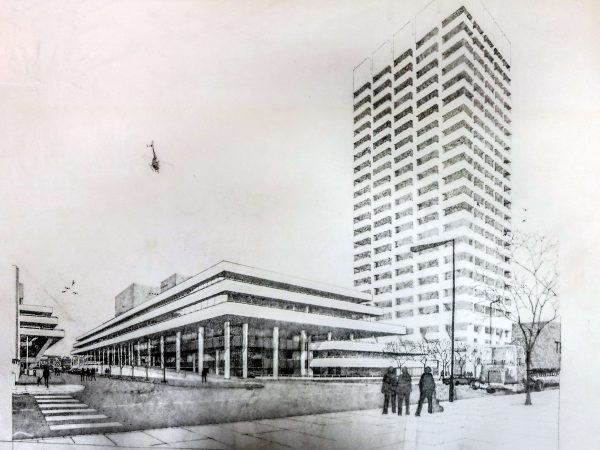
Architects sketch - RIBA archives
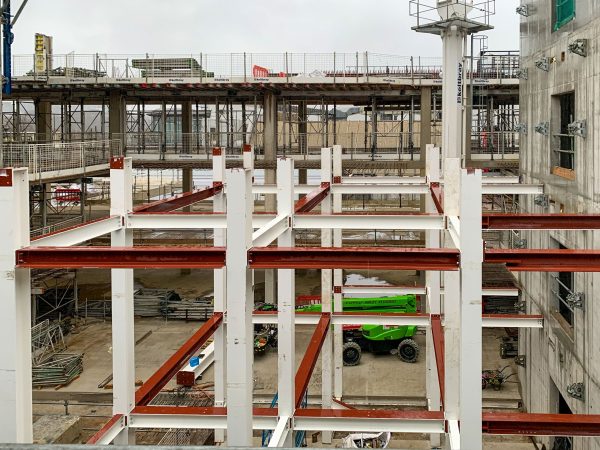
Reused steel on site
Foundations:
The building is founded on ‘Franki’ piles. These are driven, cast-in-situ concrete displacement pile with an enlarged base. A unique foundation system was design to re-use the piles with the additional load – justification of this was the first of its kind. Foundation and concrete testing was undertaken, showing that the concrete could withstand the increased load, reducing the number of new piles required. This foundation re-use scheme was nominated for the Fleming Award 2023.
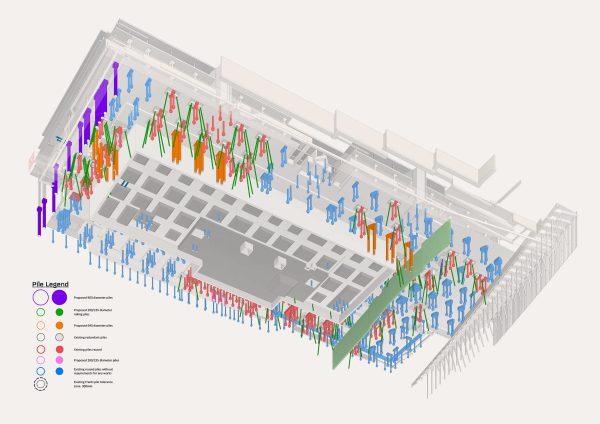
Interface between new & existing:
The RC floorplates were extended outwards by up to 17m in some areas, joining the long length of the new and existing slabs. Ensuring the forces were transferred was essential. Hydro demolition exposed the existing rebar allowing the new slab’s rebar to be coupled to the existing, with both slabs then working together.
On-site testing:
Justifying the additional load was a challenge, especially as some columns were taking up to 2.5 times the existing load. On site concrete testing showed it had a higher strength than specified and that it likely got stronger overtime. This allowed for the reduction in column strengthening required taking the number from 160 to 110. This reduction reduced cost, embodied carbon and programme.
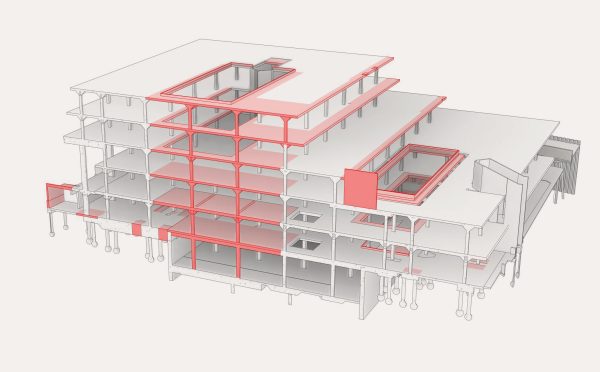
Demolition section
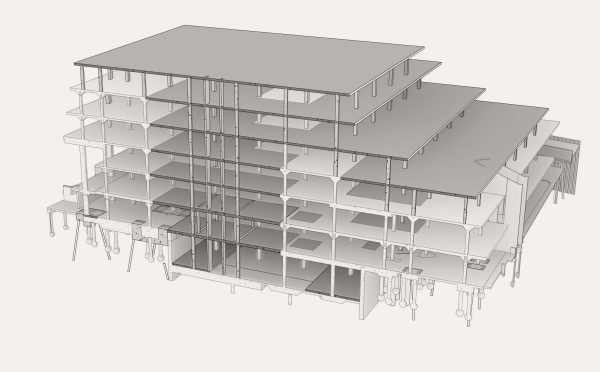
Proposed section
Topping out at 76 Southbank was a really proud moment. Totally unique floorplates, slabs of delight, in one of the coolest neighbourhoods in town. We worked hard to retain 80% of Denys Lasdun’s building whilst totally remodelling it to realise AHMM’s vision for Stanhope and Wolfe Commercial Properties.
So much engineering thought and work sits below the new top slab – 40% additional area, supported on 5 different original foundations – all reused and sweated to capacity. A landmark project in a lifetime.
Mark Tillett, Director
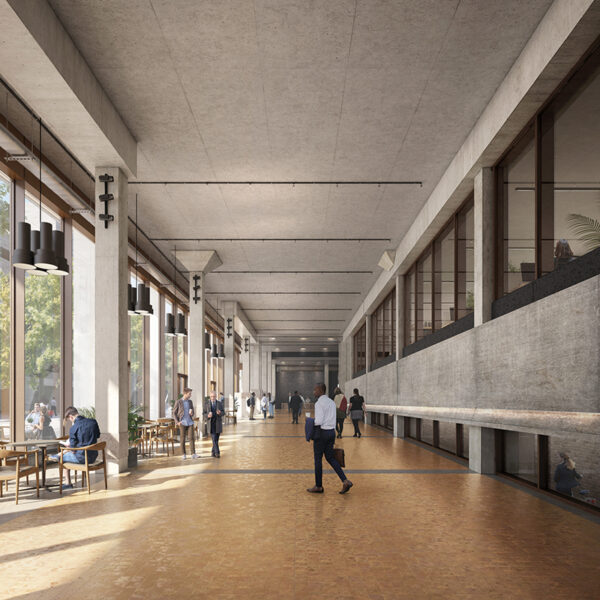
The impact
76 Southbank exemplifies how efficient design and collaborative processes can significantly impact a project of this scale. By employing a total engineering approach and conducting thorough foundation and concrete testing, HTS successfully reduced the need for column and foundation strengthening, leading to savings in cost, embodied carbon, and a streamlined programme. Furthermore, the integration of innovative systems, such as the re-use of Franki piles and re-using existing steel, further enhances the advantages of retention and preservation within the commercial sector.