Series
•How we made it: 3 Copper Square
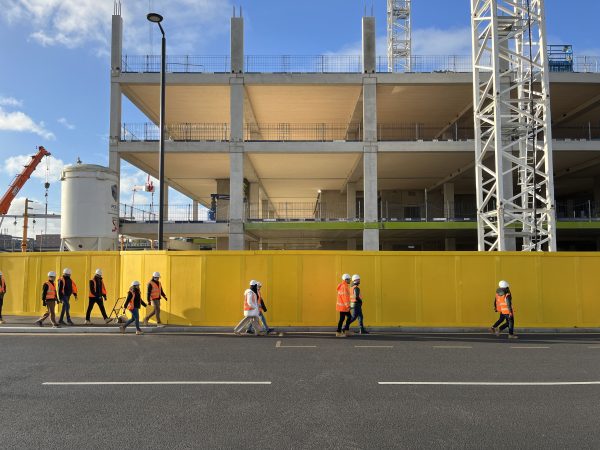
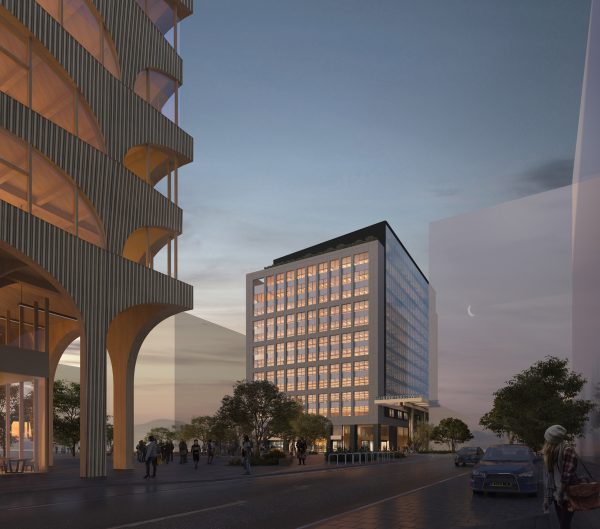
The project
Part of the Brent Cross Town masterplan, 3 Copper Square will be a new 14-storey office building constructed with a hybrid of pre-cast concrete frame and CLT panels, making it the first of its kind. A key objective for Related Argent and Barnet Council was to create a flagship commercial building whilst minimising its environmental impact and shorten construction time by utilising off-site manufacturing wherever possible. 3 Copper Square sits adjacent to the new Arbour – Brent Cross West station entrance canopy.
- Location: Barnet, London
- Client: Related Argent
- Architect: Shedkm
- Size: 30,169 m2 GIA
- Stage: In construction
- Time Frame: 2019-2025
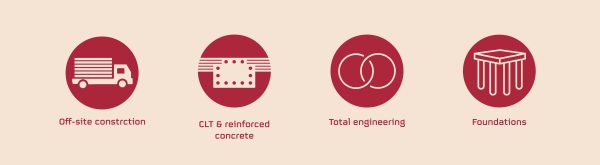
The process
Off-Site Construction
Off-site construction offers many benefits to a project including greater quality control, less material wastage and reduces programme changes. However, it also brings buildability challenges. A value engineering exercise was undertaken to reduce build costs. One outcome was to build the core from precast RC instead of in-situ, reducing costs but also reducing stiffness in the core. This results in an iterative design process to review every connection and ensure stability.
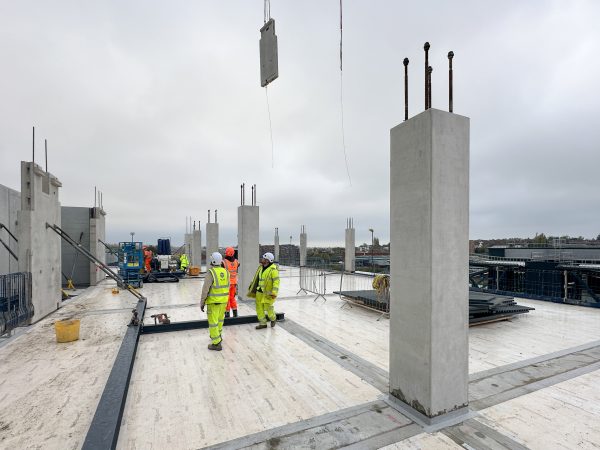
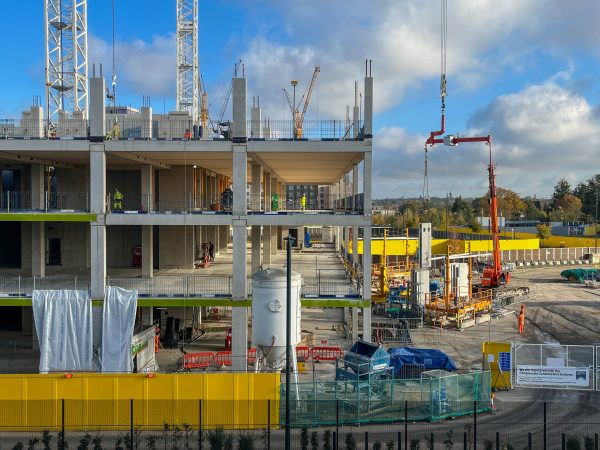
CLT & Reinforced Concrete
Different materials were considered, but a hybrid construction of PC and CLT was chosen. CLT panels reduce embodied carbon and structure weight compared to in-situ RC floor plates. They also provide a high-quality exposed finish and flush concrete soffits, unlike a full timber option.
50% GGBS cement replacement was used in PC elements. The concrete mix was designed to ensure the higher GGBS content didn’t impact fabrication time or increase embodied energy.
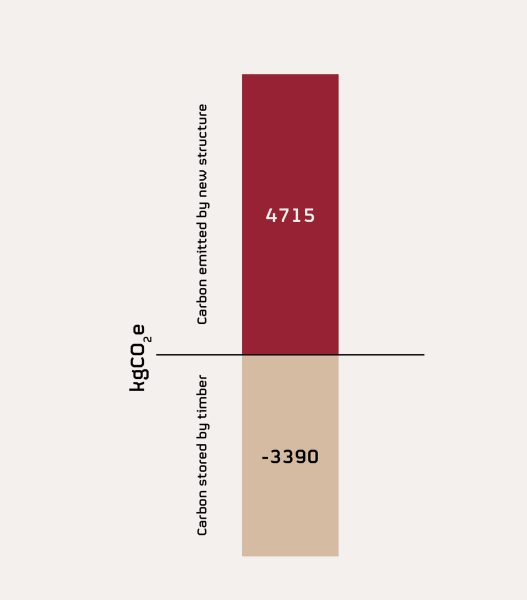
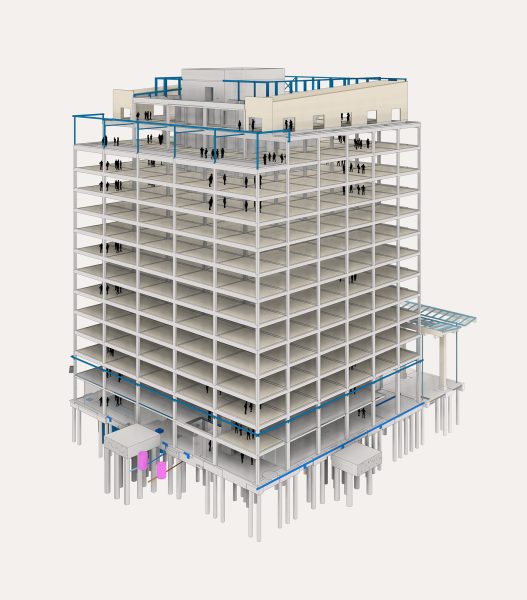
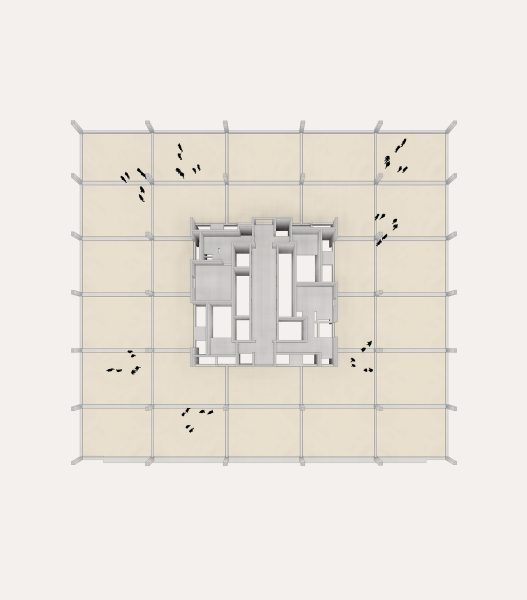
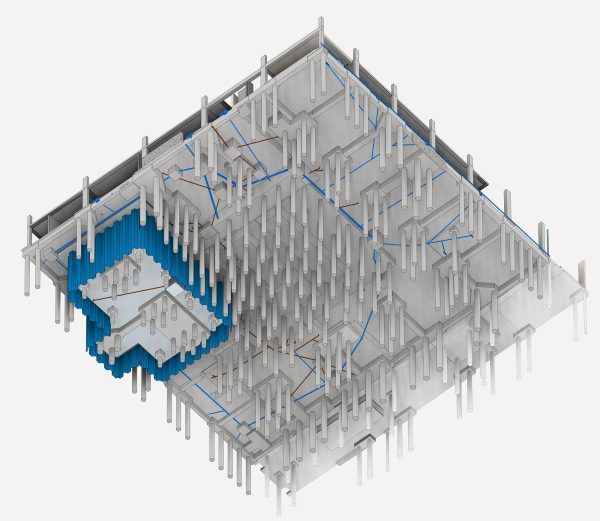
Foundations
The industrial history of the site has resulted in challenging ground conditions. Due to the depth of the made ground, the building is to be supported on piled foundations. The foundations were load tested to optimise the geotechnical design. To facilitate excavation and reduce embodied energy, sheet piles will be utilised to form the permanent basement walls.
Total Engineering
Our total engineering approach involves the design of both the temporary and permanent works. Benefits of this holistic approach include efficiencies in time, cost, programme, and embodied energy.
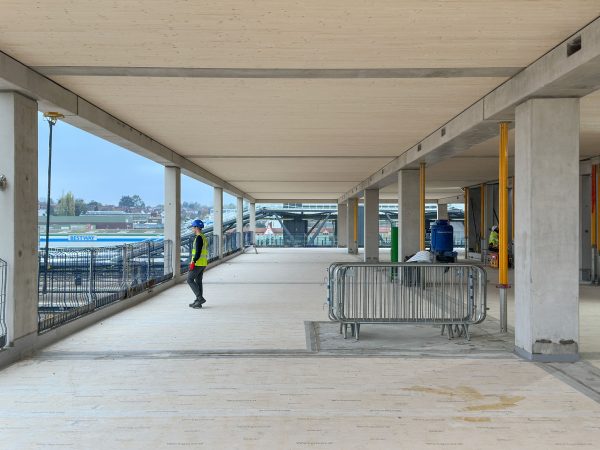
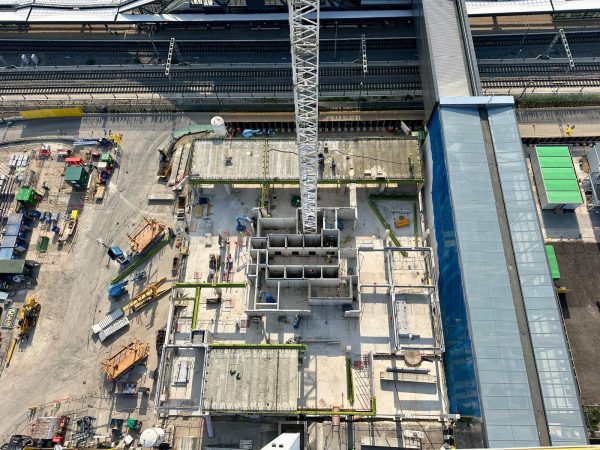
The impact
3 Copper Square will be a leading example of how a new build commercial development can achieve net zero carbon through innovative construction methods and efficient practices. The use of CLT and high GGBS cement replacement will reduce the total embodied carbon to 200kgCO2e/m², less than the LETI 2030 target. And the 10m x 7.5m floor span allows for a spacious and adaptable layout. A successful navigation of site challenges has also reduced overall cost and material wastage. 3 Copper Square is poised to set a new standard for sustainable and forward-thinking commercial spaces.