Opinion
•Steel or no steel: insights for global decarbonisation
Structural steel is a key material for modern construction, but it comes at significant environmental cost which must be addressed. Today this means scrutinising the supply chain, tracing steel, and supporting both the UK steel industry and the global transition to Direct Reduced Iron – Electric Arc Furnace (DRI-EAF) production. In our designs we prioritise sections that give maximum supply options and are setting a realistic carbon target of 1.5kgCO2e/kg overall for the steel used in our structural frames.
Steel is strong, abundant, workable, and recyclable. For many applications it is the ideal structural material. However today steelmaking is responsible for about 10% of global CO2 emissions [1, 2] and the carbon footprint of an average tonne of steel is the worst it has been in decades [3]. This is because demand for new steel keeps rising, and the dominant process for making new steel is the Blast Furnace – Basic Oxygen Furnace (BF-BOF). This process is coal powered and is highly carbon intensive; for every tonne of steel made this way, 2.3 tonnes of CO2 are released [1]
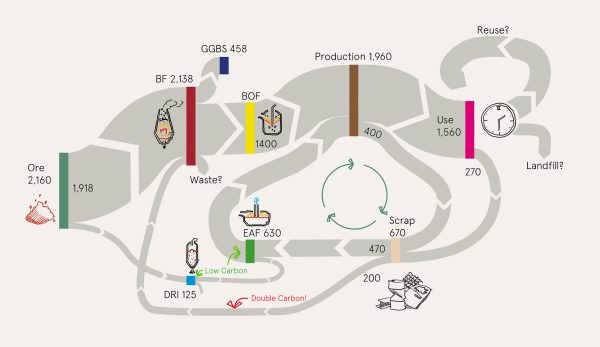
Sources: Worldsteel, Midrex
Recycled steel made from scrap in an Electric Arc Furnace (Scrap-EAF) is much lower in embodied carbon but there is only enough scrap to meet about one third of global demand [4]. Demand is also predicted to keep rising until at least 2050 so, despite scrap supply being predicted to triple in that time, the demand for steel will continue to outstrip scrap availability [4, 5].
Recycling rates are already high, and specifying recycled steel does not cause additional steel to be recycled [4]. This means that although using recycled steel can reduce embodied carbon on a project, it does not reduce the carbon footprint of the steel sector, as it does not reduce the amount of new steel being made.
By far the most powerful lever to decarbonise the industry and reduce global CO2 emissions is to promote better routes for making new steel from iron ore, reducing our reliance on highly emitting BF-BOF steelmaking [6,10].
Direct Reduced Iron – Electric Arc Furnace (DRI-EAF) steelmaking is one such route; well understood and currently accounting for 7% of global production [7]. This natural gas and electricity driven process is about 40% lower embodied carbon than BF-BOF [1]. Looking forward, green electricity and green hydrogen could completely decarbonise the process [6,10], and there are many pilot plants in Europe where this technology is also being explored [8].
At HTS our preference is to “use less stuff” and reuse where possible. We also take great pride in designing low carbon mass timber and hybrid structures. However, when steel is the best material for the job, we prioritise steel which is part of the long-term solution not the problem.
The first step here is to fully trace where our steel comes from and to seek out innovative low carbon new steel such as that produced via DRI-EAF. For embodied carbon, we prioritise standard “I” and “H” sections to give maximum supply options, and in our specifications we are targeting a maximum average of 1.5kgCO2e/kg for the structural steel frame. This is based on IStructE carbon values and a 50/50 split of Scrap-EAF and BF-BOF steel [9]. This value not only supports domestic steelmaking capacity but can also be achieved using DRI-EAF steel.
The complexity and variety within the steel supply chain makes accurate carbon reporting an ongoing challenge across all sectors, so as well as targeting a carbon value our approach prioritises transparency and supports domestic and global innovation.
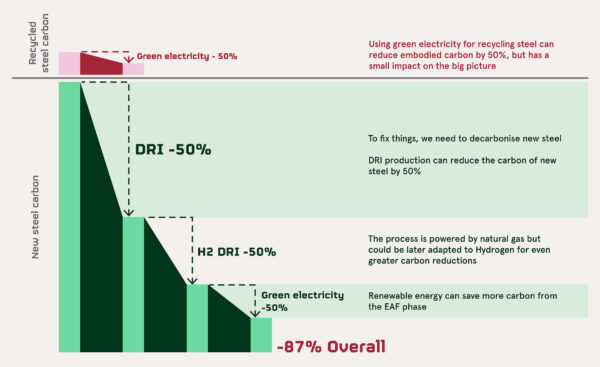
[1] World Steel in Figures 2024 – WorldSteel
[2] CO2 Emissions in 2022 – IEA 2022
[3] Sustainability Indicators 2023 – WorldSteel
[4] Fact Sheet On Scrap 2021 – WorldSteel
[5] A Bright Future for UK Steel – Allwood – 2016
[6] Implementation of RFNBOs targets in industry pursuant Art.22a RED 2023/2413 – Eurofer
[7] Midrex Stats Book 2022 – Midrex
[8] Hydrogen in Steel Production – What is Happening in Europe part two – Bellona.org
[9] How To Calculate Embodied Carbon, IStructE, Second Edition
[10] The Potential of Hydrogen for Decarbonising Steel Production – European Parliament 2020